Hydraulic systems are integral to a wide range of machinery, from excavators and forklifts to hydraulic presses and construction equipment. At the heart of these systems lies hydraulic fluid, which plays a crucial role in lubrication, cooling, sealing, and power transmission. Regularly checking the hydraulic fluid is essential to ensure that these systems operate efficiently and safely.
The importance of hydraulic fluid goes beyond its basic function. Low fluid levels, contamination, or degraded oil quality can lead to system failures, reduced performance, and costly repairs. That’s why understanding how to properly check hydraulic fluid is a critical skill for operators and maintenance personnel.
In this guide, we’ll walk you through the step-by-step process of checking hydraulic fluid, from assessing the oil level and quality to identifying potential issues. Whether you’re working with a hydraulic press, excavator, or any other heavy machinery, these techniques will help you keep your equipment running smoothly and avoid costly downtime.
Why is it Important to Check Hydraulic Fluid?
Hydraulic fluid plays a pivotal role in the functionality of hydraulic systems. Without proper fluid maintenance, the machinery can experience reduced efficiency, premature wear, and even catastrophic failure. Here are the key reasons why checking hydraulic fluid regularly is essential:
Hydraulic Fluid Functions in the System
Hydraulic fluid serves multiple critical purposes in a hydraulic system:
- Lubrication: It reduces friction between moving parts, minimizing wear and tear on the system components.
- Cooling: The fluid absorbs heat generated during operation and helps maintain optimal operating temperature, preventing overheating.
- Sealing: It forms a seal that enables pressure to build up in the hydraulic system, ensuring smooth operation.
- Power Transmission: Hydraulic fluid transmits the energy needed to perform mechanical work, enabling the movement of equipment such as hydraulic presses, excavators, and lifts.
Without hydraulic fluid, or with degraded fluid, the system will be unable to perform these functions effectively, leading to decreased operational efficiency.
Impact of Low Fluid Levels
Low hydraulic fluid levels can have several adverse effects:
- Loss of Pressure: The hydraulic system relies on a certain amount of fluid to maintain proper pressure. If the fluid level is too low, the system may not generate enough pressure, leading to sluggish performance and potential failure of critical components.
- Increased Wear: Insufficient lubrication and cooling can accelerate wear on the pump, valves, and actuators, causing parts to deteriorate faster and requiring more frequent repairs or replacements.
- System Overheating: Low fluid levels reduce the system’s ability to absorb heat, leading to overheating. This can cause oil to break down more quickly and result in poor performance or even component damage.
The Risks of Contaminated Hydraulic Fluid
Hydraulic fluid can become contaminated over time by dirt, water, or wear particles from the system itself. Contaminated fluid can:
- Cause Blockages: Contaminants can clog filters, valves, and lines, restricting fluid flow and causing erratic machine behavior.
- Accelerate Wear: Abrasive particles in the fluid can cause excessive wear on internal components like pumps and seals, leading to breakdowns and costly repairs.
- Degrade Performance: The presence of water or other impurities can change the chemical composition of the fluid, affecting its ability to lubricate, cool, and transmit power efficiently.
Degraded Fluid Quality
As hydraulic fluid ages, its properties can degrade, making it less effective at performing its duties:
- Viscosity Loss: Over time, fluid can lose its ideal viscosity, which can lead to improper lubrication and inefficient power transmission. This can affect the system’s responsiveness and overall performance.
- Oxidation: Hydraulic fluid exposed to air and heat can oxidize, leading to the formation of sludge, varnish, and acids. These byproducts can impair fluid flow and damage sensitive components.
- Color Change: Healthy hydraulic fluid is typically clear or slightly amber. If the fluid turns dark brown or black, it could be an indication of contamination or thermal degradation, signaling the need for replacement.
Avoiding Expensive Repairs and Downtime
Neglecting to regularly check hydraulic fluid can lead to a cascade of problems. Not only can low fluid levels or poor quality lead to immediate system failures, but it can also cause long-term damage to components. Over time, this damage can result in costly repairs, extended downtime, and a significant loss of productivity.
By checking the hydraulic fluid regularly, you can ensure the system operates at peak performance, preventing the need for expensive maintenance and minimizing the risk of unexpected breakdowns.
Basic Steps for Checking Hydraulic Fluid
Checking hydraulic fluid is a straightforward process, but it requires attention to detail to ensure accurate results. By following these steps, you can properly assess the oil level and quality, ensuring that your hydraulic system runs efficiently and effectively.
Prepare for the Inspection
Before you begin, make sure you’re taking the proper precautions to ensure safety and accuracy:
- Turn Off the Equipment: Always turn off the hydraulic system and allow the machine to cool down if it’s been running. This is especially important for checking oil levels, as a hot system can result in inaccurate readings.
- Clear the Area: Make sure the area around the hydraulic system is clean. Avoid introducing dirt or contaminants into the hydraulic system, as they can degrade the fluid and cause long-term damage.
Step 1: Locate the Hydraulic Fluid Reservoir and Dipstick
Each hydraulic system will have a reservoir (oil tank) for the hydraulic fluid, and most will have a dipstick or a sight glass to check the fluid level. The location of these components will vary by equipment type, so refer to the manufacturer’s manual for precise instructions.
- Dipstick Method: Many systems use a dipstick to measure the fluid level. Simply pull the dipstick out, wipe it clean with a rag, and reinsert it back into the reservoir. Then, pull it out again to check the oil level against the minimum and maximum marks on the dipstick.
- Sight Glass Method: Some hydraulic systems have a transparent sight glass built into the reservoir, allowing you to visually check the fluid level. Ensure the fluid is within the indicated range. If the level is low, add more fluid.
Step 2: Check the Fluid Level
It’s important to regularly check the hydraulic fluid level to prevent operational issues.
- Correct Fluid Level: The fluid level should fall within the manufacturer’s recommended range. A low fluid level can cause the system to operate inefficiently, leading to reduced performance and potential system damage.
- Refilling the Fluid: If the fluid level is below the recommended range, carefully top it up with the correct type of hydraulic fluid specified by the manufacturer. Be cautious not to overfill, as this could lead to excessive pressure and leaks.
Step 3: Inspect the Fluid’s Appearance and Quality
The appearance of the hydraulic fluid is one of the best indicators of its health. Healthy hydraulic fluid should be clean, clear, and within the proper viscosity range.
- Check for Contamination: Examine the fluid for any signs of contamination, such as dirt, water, or metal particles. Contaminants can cause internal damage to the hydraulic system and compromise performance.
- Oil Color: Fresh hydraulic fluid typically has a clear or slightly amber color. Over time, however, the fluid may darken as it becomes contaminated or degraded. If the fluid turns black or muddy, it’s a sign that it needs to be replaced.
- Consistency: The fluid should flow smoothly and without sludge. Thick, sludgy oil indicates that the fluid has broken down and may no longer be able to properly lubricate and cool the system.
- Smell: If the hydraulic fluid has a burnt odor, this may indicate overheating or degradation of the oil, and it likely needs to be replaced.
Step 4: Check for Leaks and Other Signs of Damage
While checking the fluid, it’s also important to inspect the entire hydraulic system for leaks or visible damage:
- Leaks Around Hoses and Fittings: Leaks can lead to fluid loss and reduced efficiency. Look for drips, wet spots, or discoloration around hose connections, seals, and fittings.
- Damaged Components: If you notice any broken or damaged components, such as hoses or valves, these should be repaired or replaced to prevent further issues.
Step 5: Check the Hydraulic Fluid Temperature
The operating temperature of hydraulic fluid can greatly affect its performance. Typically, hydraulic fluid should operate within a temperature range of 120°F to 150°F (49°C to 66°C), but this can vary depending on the specific equipment and manufacturer’s recommendations.
- Overheating Signs: If the fluid is too hot, it may indicate that the system is working too hard, or the cooling system is malfunctioning. In such cases, the oil may break down, causing it to lose its effectiveness.
- Coolant Systems: If the temperature is too high, check the radiator or cooling system to ensure it’s functioning properly.
Step 6: Record the Findings and Schedule Maintenance
After completing the inspection, record the oil level, condition, and any issues found. This record can help track trends in the system’s health over time and identify potential issues before they become critical.
- Regular Maintenance: If the fluid is contaminated or degraded, schedule a fluid replacement as soon as possible. Regular fluid changes and filter replacements are essential for maintaining hydraulic system efficiency.
Checking Hydraulic Fluid for Different Equipment
While the general process for checking hydraulic fluid remains consistent, different types of machinery require specific approaches due to varying system designs and operational demands. Below, we break down how to check hydraulic fluid for some of the most common equipment types, including hydraulic presses, excavators, and forklifts.
Hydraulic Press
Hydraulic presses, used in manufacturing and heavy industries, require a carefully maintained hydraulic system to ensure precision and power transmission.
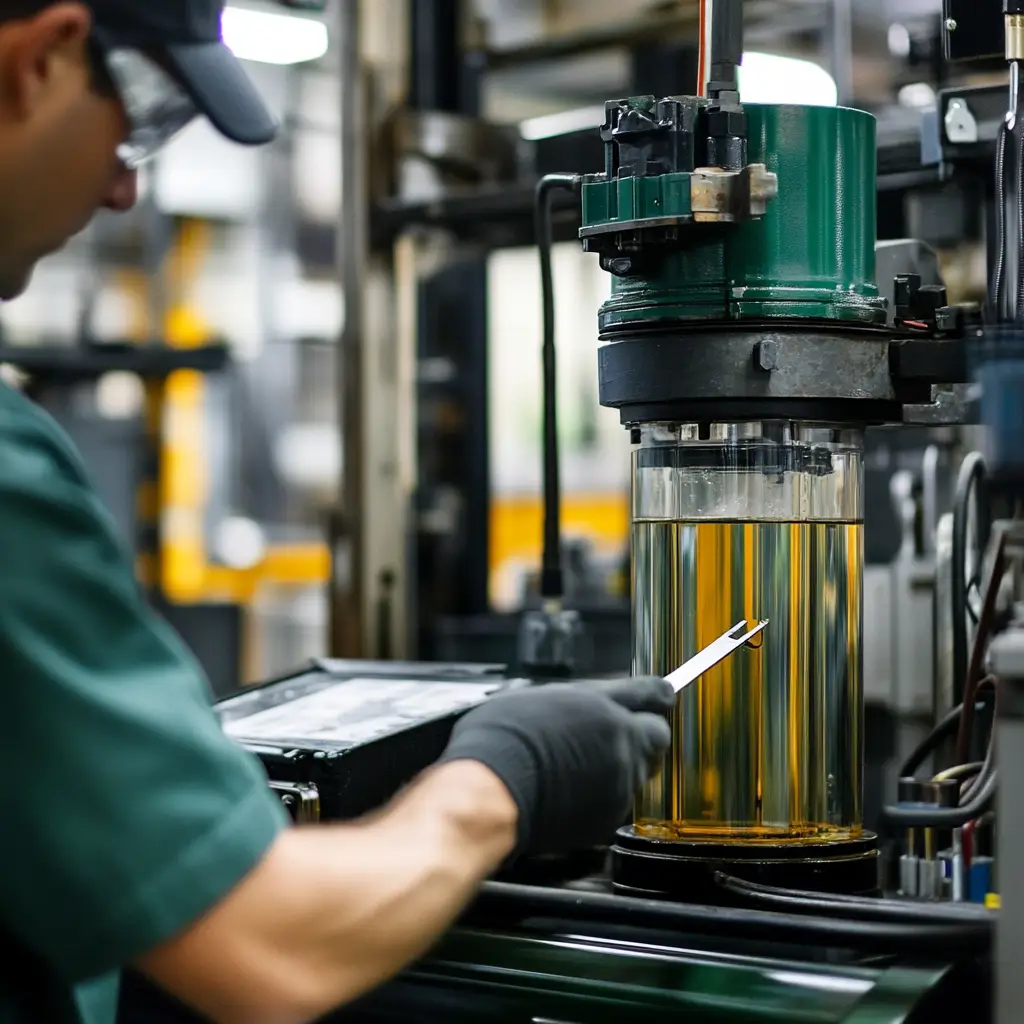
Here’s how to check the hydraulic fluid for a press:
Step 1: Turn Off the Press and Let it Cool
Before checking the hydraulic fluid in a press, always power down the machine and allow it to cool. This helps prevent burns from hot fluid and ensures that you get an accurate reading.
Step 2: Check the Fluid Level Using the Sight Glass or Dipstick
Many hydraulic presses have a sight glass to visually inspect the fluid level. If your press uses a dipstick, remove it, clean it, and reinsert it to measure the fluid. The oil should be between the minimum and maximum marks.
Step 3: Assess Fluid Condition
The quality of the hydraulic fluid is just as important as the level. If the fluid is dark, foamy, or contains visible particles, it may be time to replace it. Also, check for any unusual odors or excessive heat, which could indicate contamination or overheating.
Step 4: Check the Filter
In a hydraulic press, the filter plays a critical role in preventing contaminants from damaging the system. Regularly inspect and clean or replace the filter to ensure optimal fluid quality.
Excavator
Excavators are heavy-duty machines that rely heavily on hydraulic systems for lifting, digging, and maneuvering.
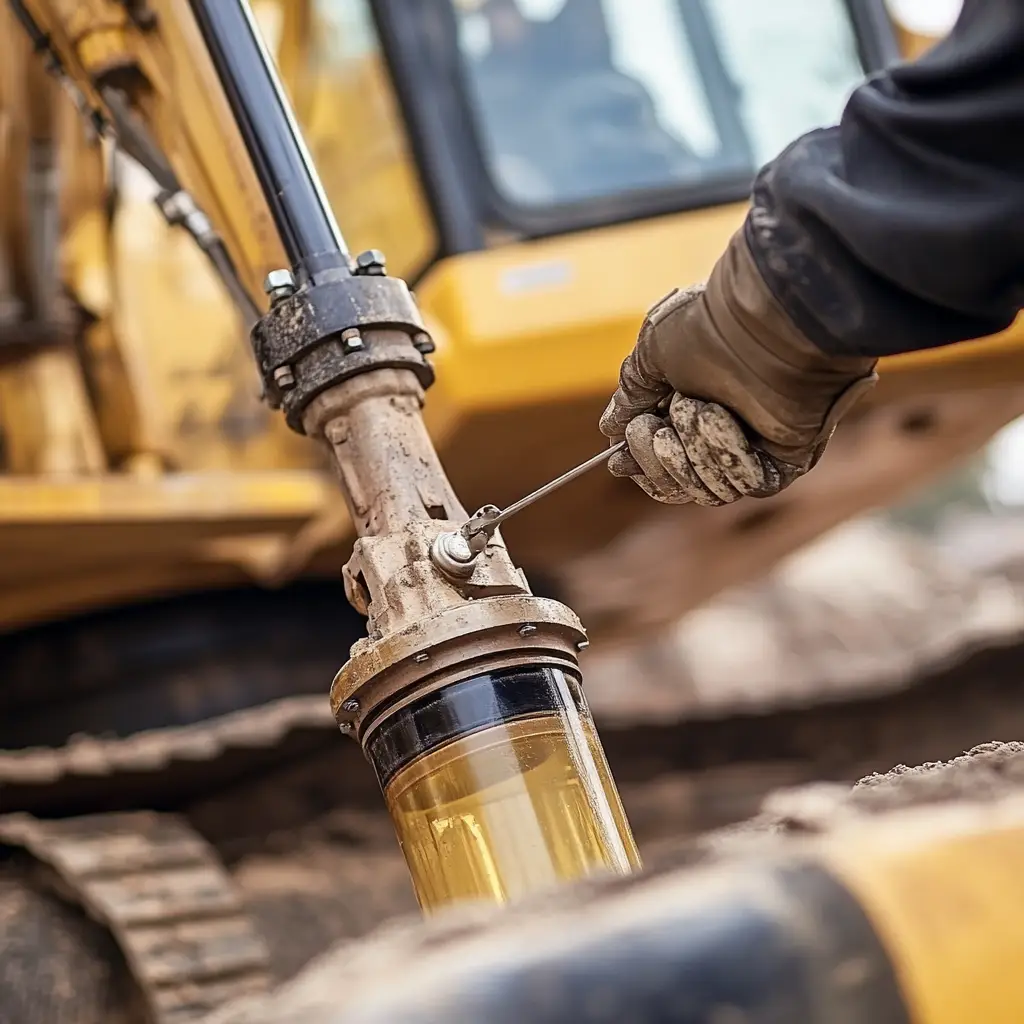
Checking hydraulic fluid in these machines is crucial for maintaining optimal performance.
Step 1: Park the Excavator on a Flat Surface
Ensure that the excavator is parked on level ground before checking the fluid. This will give an accurate reading of the fluid level and prevent any uneven distribution of the oil inside the tank.
Step 2: Locate the Fluid Reservoir and Dipstick
In most excavators, the hydraulic fluid reservoir is located near the engine or in a dedicated compartment. Use the dipstick to check the fluid level, making sure it’s between the minimum and maximum indicators.
Step 3: Inspect Fluid Quality
After checking the level, inspect the oil for signs of contamination. If the fluid is murky, has a burnt smell, or shows a milky appearance, it may be contaminated with water or dirt. If contamination is found, the fluid should be changed.
Step 4: Inspect the Hydraulic Lines and Filter
Hydraulic lines should be checked for any signs of leaks or wear. Additionally, the hydraulic filter should be cleaned or replaced regularly to prevent debris from circulating in the system.
Forklifts
Forklifts use hydraulic fluid to power their lifting and tilting mechanisms. Regular fluid checks are vital to prevent malfunctions and ensure safe operation.
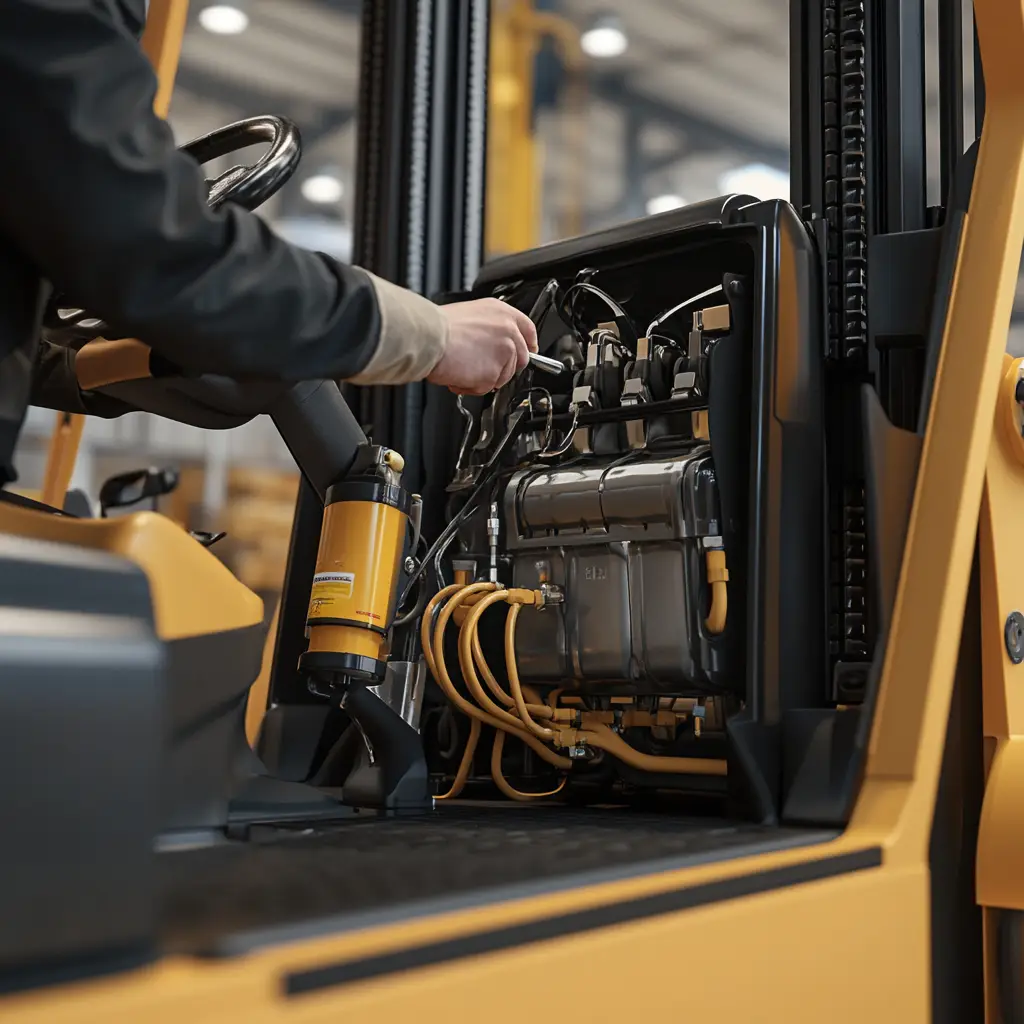
Step 1: Park the Forklift and Turn Off the Engine
For accurate measurements, park the forklift on a level surface and ensure the engine is off. Wait for the hydraulic fluid to settle for a more precise reading.
Step 2: Locate the Hydraulic Fluid Reservoir
Forklifts typically have a reservoir located either in the front of the truck or near the engine. Check the fluid level using the dipstick or sight glass. Make sure the level is within the recommended range.
Step 3: Assess Fluid Condition
If the fluid appears dirty, foamy, or has a burnt odor, it indicates that the oil has deteriorated and may need to be replaced. Clean fluid should be clear and slightly amber in color.
Step 4: Check the Hydraulic Hoses and Connections
Inspect the hoses for signs of leaks, wear, or damage. Ensure that all connections are tight and secure to avoid fluid loss.
Other Equipment
For other types of machinery, such as loaders, dump trucks, and more, the basic steps for checking hydraulic fluid remain similar, but the specifics may vary:
- Consult the Manufacturer’s Manual: Always refer to the equipment’s user manual for the exact procedure for checking hydraulic fluid. Some systems may have specific requirements, such as pressure tests or more frequent checks depending on usage.
- Routine Maintenance: In high-use machinery, such as loaders or mining equipment, more frequent fluid checks may be necessary due to the heavy load on the hydraulic system.
By understanding how to check hydraulic fluid for different types of equipment, you can ensure that each machine operates optimally, preventing downtime and costly repairs.
Common Issues and Solutions When Checking Hydraulic Fluid
Despite regular maintenance, hydraulic systems can still encounter issues with fluid levels, quality, and performance. Below are some of the most common problems you may face when checking hydraulic fluid, along with their potential causes and solutions.
Low Hydraulic Fluid Levels
One of the most common issues is low hydraulic fluid levels, which can lead to a decrease in pressure and efficiency.
Possible Causes:
- Leaks in the system: Over time, seals and hoses can wear out, leading to fluid leaks.
- Evaporation or contamination: In extreme conditions, the hydraulic fluid can evaporate or become contaminated, reducing its volume.
- Improper filling: If the system was not properly topped off after maintenance, the fluid level might remain too low.
Solutions:
- Inspect for Leaks: Check all hoses, seals, and connections for signs of leaks. If you find any, replace or repair the faulty parts immediately.
- Top Off the Fluid: Ensure the fluid is added to the correct level according to the manufacturer’s specifications. Always use the recommended type of hydraulic fluid for your equipment.
- Check the Fill Cap and Seal: Ensure the cap is securely closed to avoid fluid loss during operation.
Contaminated Hydraulic Fluid
Contaminated hydraulic fluid can cause significant damage to the system, including clogged filters, pump failure, and poor performance.
Possible Causes:
- Dirt or debris entering the system: Contaminants can get into the system through improperly sealed reservoirs or during fluid replacement.
- Moisture contamination: Water can enter the hydraulic fluid, particularly if the system is exposed to rain or extreme humidity.
- Degradation of Fluid Quality: Over time, hydraulic fluid can break down due to heat, oxidation, or chemical reactions, leading to the formation of sludge or varnish.
Solutions:
- Change the Fluid: If the fluid appears dirty, discolored, or has a burnt smell, it’s time to replace it. Always dispose of the old fluid properly, according to local regulations.
- Check Filters: Regularly clean or replace the hydraulic filters to prevent contaminants from circulating in the system. Consider upgrading to finer filtration if your equipment operates in harsh conditions.
- Monitor Water Contamination: If water contamination is detected, inspect the system for leaks in seals or other components that may allow water ingress.
Overheating Hydraulic Fluid
Excessive heat can cause hydraulic fluid to break down quickly, leading to reduced performance, damage to components, and failure of the hydraulic system.
Possible Causes:
- Excessive load: Operating the equipment beyond its capacity can cause the fluid to overheat.
- Faulty cooling system: A malfunction in the cooling system, such as a clogged radiator or a broken fan, can prevent the fluid from being properly cooled.
- Incorrect fluid type: Using a fluid that isn’t designed for the temperature conditions can cause overheating.
Solutions:
- Reduce Load and Idle Time: Ensure the equipment is operating within its recommended load limits. If the system is under heavy load, allow for cooling periods to prevent overheating.
- Inspect Cooling System: Check the cooling fans, radiators, and oil coolers for clogs or malfunctions. Clean or replace components as necessary.
- Use the Correct Hydraulic Fluid: Make sure the fluid used matches the manufacturer’s recommended specifications for the temperature and operational conditions.
Foam Formation in Hydraulic Fluid
Foaming in hydraulic fluid can impair the system’s ability to generate pressure, leading to inefficient performance.
Possible Causes:
- Contamination with air: Air entering the system through leaks or improperly filled reservoirs can cause foam to form in the hydraulic fluid.
- Incorrect fluid level: If the fluid is too low, the pump may draw in air, creating foam.
- High fluid temperature: Excessive heat can cause air to become trapped in the fluid, resulting in foaming.
Solutions:
- Check for Leaks: Inspect all seals and hoses for leaks that may allow air to enter the system. Replace faulty seals or tighten loose connections.
- Maintain Proper Fluid Level: Ensure that the hydraulic fluid is topped off to the correct level. Do not overfill, as this can also contribute to foam formation.
- Monitor Fluid Temperature: Keep the system temperature in check by preventing overloading and ensuring the cooling system is functioning properly.
Unusual Noises or Vibrations
Hearing strange noises or noticing vibrations during operation could indicate a problem with the hydraulic fluid or system.
Possible Causes:
- Low fluid level: If the fluid is too low, air may be introduced into the system, leading to cavitation, which causes abnormal noises.
- Contaminated fluid: Contaminants in the fluid can cause internal damage, leading to noise or vibrations during operation.
- Pump or motor issues: If the pump or motor is malfunctioning, it can cause irregular noise, which may also be related to poor fluid quality or level.
Solutions:
- Top Off the Fluid: Ensure the fluid level is correct, and top it off if necessary. If the fluid level is fine but the problem persists, check the fluid quality and replace it if it appears contaminated.
- Check for Contamination: Inspect the fluid for any visible signs of contaminants. If necessary, replace the fluid and clean the system to prevent further damage.
- Inspect the Pump: If the problem continues after addressing the fluid level and contamination, check the pump and motor for wear or damage. Repair or replace the faulty components as needed.
Best Practices for Maintaining Hydraulic Fluid and the Hydraulic System
Proper maintenance of hydraulic fluid and the hydraulic system as a whole is essential to ensure long-term reliability, optimal performance, and to avoid costly repairs. Here are some best practices to keep your hydraulic system running smoothly:
Regularly Check Fluid Levels and Quality
- Routine Inspections: Set a regular schedule for checking hydraulic fluid levels, especially before and after heavy use. This ensures that fluid levels are maintained and any issues can be identified early.
- Check Fluid Quality: In addition to checking the fluid level, regularly assess the quality of the hydraulic fluid. Look for signs of contamination, discoloration, or foam. Contaminated fluid can cause damage to the pump, valves, and seals, so it’s important to replace fluid that is no longer in good condition.
- Use the Right Fluid: Always use the manufacturer-recommended hydraulic fluid. Different systems require specific fluid types based on their viscosity, additive package, and temperature range. Using the wrong type of fluid can result in poor performance and increased wear on system components.
Keep the System Clean
- Seal the Reservoir: Ensure that the hydraulic fluid reservoir is properly sealed to prevent contaminants like dirt, dust, and water from entering the system.
- Use Filters: Hydraulic filters are designed to trap contaminants, but they need to be cleaned or replaced regularly. Follow the manufacturer’s guidelines for filter replacement schedules.
- Clean Fluid Fill Ports: When adding fluid, always clean the fill port and surrounding area before opening the cap. Even small amounts of dirt can cause significant damage to the system if introduced into the fluid.
Maintain Proper Fluid Temperature
- Monitor Temperature: Hydraulic fluid temperature should remain within the range specified by the equipment manufacturer. Overheating can degrade fluid quality and lead to faster wear on components.
- Install Cooling Systems: In high-demand applications, consider adding a cooling system, such as a heat exchanger or radiator, to keep the fluid temperature under control.
- Prevent Overheating: Avoid prolonged heavy loads or excessive operation without breaks, as this can increase the temperature of the hydraulic fluid.
Address Leaks Immediately
- Inspect Hoses and Seals Regularly: Hydraulic systems are prone to leaks, especially around hoses, seals, and fittings. Check these components regularly for any signs of wear or damage, such as cracks, bulges, or dampness.
- Replace Damaged Components: If you detect any leaks, address them immediately by replacing damaged hoses or seals. Even small leaks can quickly escalate and cause major problems if not fixed promptly.
- Use Leak Detection Tools: Some systems may benefit from using ultrasonic or infrared tools to detect leaks that are not immediately visible. These tools can help identify hidden leaks that may go unnoticed during routine inspections.
Follow Manufacturer’s Maintenance Schedule
- Adhere to the Maintenance Manual: Each hydraulic system has its own set of maintenance guidelines, including recommended fluid change intervals, filter replacement, and other routine checks. Always follow the manufacturer’s maintenance schedule to prevent premature failure of system components.
- Record Keeping: Maintain detailed records of all maintenance activities, including fluid changes, filter replacements, and any repairs. This helps you track the condition of the system over time and can be invaluable if problems arise in the future.
Train Personnel on Proper Maintenance
- Operator Training: Ensure that all personnel operating hydraulic equipment are properly trained on how to check fluid levels, assess fluid quality, and identify potential issues.
- Service Personnel: Have qualified technicians perform more in-depth inspections and maintenance, including fluid replacements, pressure testing, and system diagnostics.
Keep an Eye on Fluid Contamination
- Use Clean Containers: When adding new fluid, ensure it is stored in a clean, sealed container. Never pour fluid directly from the original container into the system, as it may contain contaminants.
- Monitor for Moisture: Be mindful of the potential for moisture entering the hydraulic system, especially in areas with high humidity or in outdoor operations. Moisture can lead to rust and premature wear. Installing desiccant breathers or using moisture-absorbing additives can help mitigate this risk.