Introduction
Hydraulic systems are fundamental to a multitude of industries, including construction, manufacturing, and aviation, and they serve as the backbone of many machines. Understanding these systems, specifically the maximum hydraulic pressure they can handle, is crucial to ensure their safe and efficient operation. In this article, we delve into this complex topic to provide a comprehensive understanding of the factors influencing maximum hydraulic pressure.


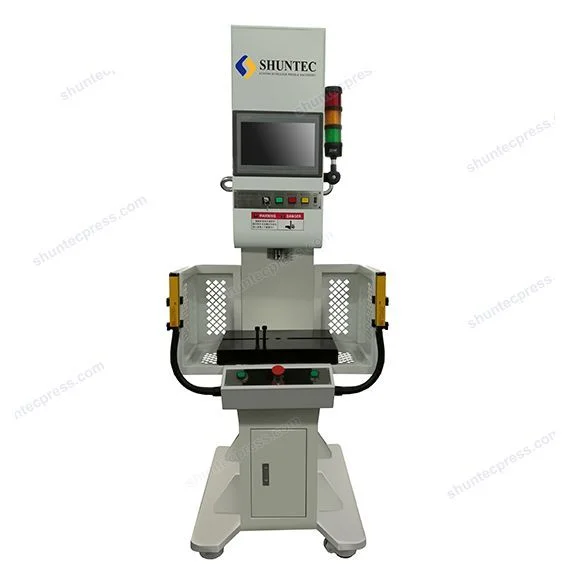
Understanding Hydraulic Pressure
Before diving into the specifics, it’s important to clarify what we mean by hydraulic pressure. Simply put, hydraulic pressure is the force per unit area exerted by a fluid in a hydraulic system. It’s this pressure that allows hydraulic systems to do work, whether that’s lifting a heavy load or moving a machine part.
Hydraulic pressure can be broadly classified into two types: static and dynamic. Static hydraulic pressure is the pressure when the fluid is at rest, while dynamic pressure is the pressure when the fluid is in motion. The maximum hydraulic pressure typically refers to the highest dynamic pressure the system can handle without causing damage.
What Determines the Maximum Pressure in a Hydraulic System?
The maximum pressure in a hydraulic system is primarily determined by the pressure rating of the system, which is the highest pressure it is designed to handle. Various components of the system contribute to this maximum pressure, including the pump, valves, actuators, and hoses.
- Pump: The hydraulic pump is what generates the pressure in the system. Its maximum operating pressure, determined by its design and construction, sets a limit on the overall system pressure.
- Valves: Valves control the flow and direction of the hydraulic fluid. The pressure rating of these valves must be adequate to handle the maximum system pressure.
- Actuators: Actuators, such as hydraulic cylinders or motors, transform hydraulic pressure into mechanical work. Their pressure rating is often a determining factor in the system’s maximum pressure.
- Hoses and fittings: These transport the hydraulic fluid throughout the system. If they can’t handle the system’s maximum pressure, they could rupture, leading to leaks or system failure.
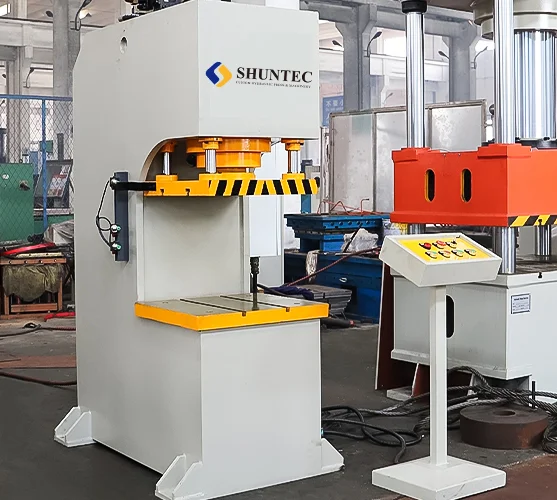
What Is the Maximum Pressure for Hydraulic Fluid?
Hydraulic fluid plays a vital role in transmitting pressure within a hydraulic system. While it doesn’t directly determine the system’s maximum pressure, its characteristics heavily influence how effectively the system can operate at high pressures.
Typically, hydraulic fluid can handle pressure ranges from a few hundred to several thousand pounds per square inch (psi). However, this varies based on several factors:
- Viscosity: The viscosity of the hydraulic fluid affects its flow characteristics and its ability to maintain a seal under pressure. Both high and low viscosity can lead to problems at high pressures.
- Temperature: High temperatures can thin the hydraulic fluid, reducing its pressure handling capabilities. On the other hand, cold temperatures can increase its viscosity, leading to inefficient operation.
- Contamination: Contaminants can cause damage to the system’s components and reduce the hydraulic fluid’s ability to transmit pressure effectively.
How Do You Find the Maximum Pressure of a Cylinder?
The maximum pressure a cylinder can handle, often referred to as its pressure rating, is typically provided by the manufacturer. However, it can also be calculated using the formula P = F/A, where P is the pressure, F is the force exerted by the cylinder, and A is the surface area of the piston.
For instance, if a hydraulic cylinder is designed to exert a force of 10,000 pounds and the piston’s surface area is 20 square inches, the maximum pressure the cylinder can handle is 10,000/20 = 500 psi. It’s crucial to never exceed a cylinder’s maximum pressure rating, as this could lead to failure of the cylinder or other system components.
How Do You Find the Pressure in Hydraulics?
Measuring pressure in a hydraulic system is crucial for maintaining optimal performance and preventing damage. Pressure can be measured using various tools, including pressure gauges, transducers, and sensors.
A step-by-step guide to measure pressure in a hydraulic system is as follows:
- Identify the appropriate measurement points: These are typically at the pump, actuators, and valves, where pressure variations are most critical.
- Install the appropriate pressure measurement device: Pressure gauges are typically used for manual measurements, while transducers and sensors can provide continuous, real-time data.
- Record the pressure readings: For manual measurements, this involves visually inspecting the gauge and recording the reading. For digital devices, the data may be stored electronically and can often be analyzed using specialized software.
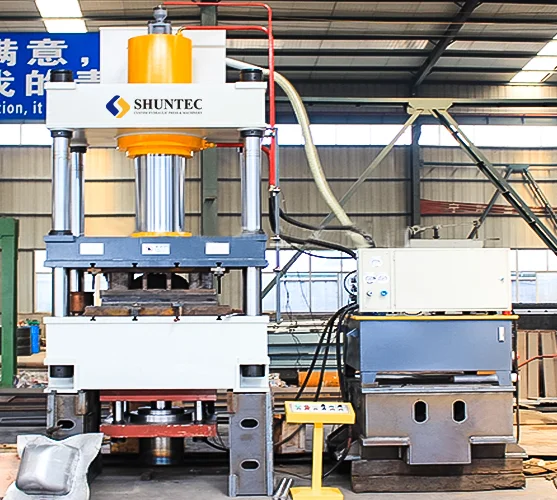
What Factors Affect Hydraulic Pressure?
Several factors can influence hydraulic pressure, including load changes, temperature variations, fluid conditions, and component wear and failure.
- Load changes: As the load on a hydraulic system changes, so too does the required pressure. Greater loads require higher pressure, so sudden load changes can lead to pressure spikes.
- Temperature variations: As previously mentioned, temperature changes can affect the viscosity of the hydraulic fluid, thereby affecting the system’s pressure. Regular monitoring of fluid temperature is essential to maintain optimal pressure.
- Fluid conditions: Contaminated or degraded fluid can lead to inefficient operation and increased pressure. Regular fluid checks and changes are necessary to prevent these issues.
- Component wear and failure: Over time, components such as seals, hoses, and valves can wear out or fail, causing leaks and drops in pressure. Regular maintenance and component replacement can help prevent these issues.
Conclusion
Understanding the maximum hydraulic pressure of a system is critical to ensuring its efficient and safe operation. This involves not only knowing the pressure ratings of individual components but also regularly monitoring and maintaining the system. As we’ve seen, factors such as load changes, temperature variations, fluid conditions, and component wear can significantly impact hydraulic pressure, so it’s essential to keep these in check to prevent potential issues.