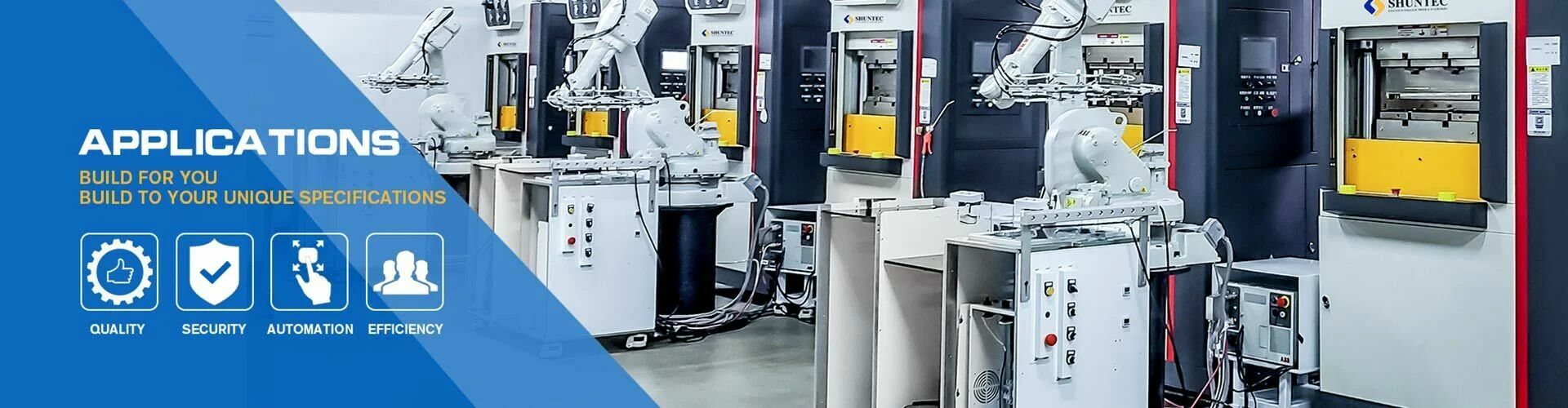
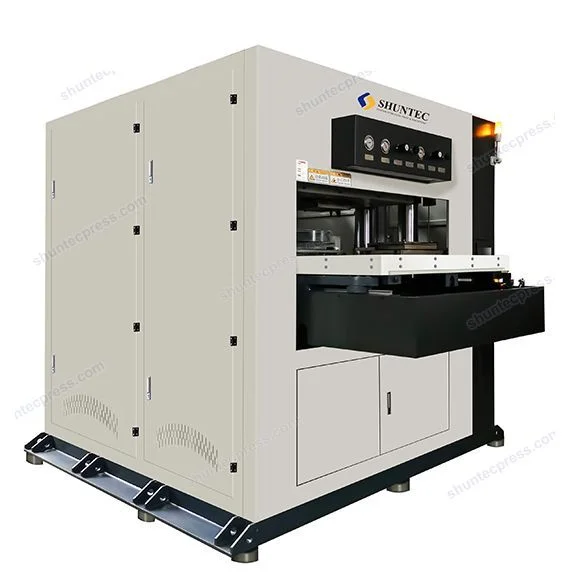
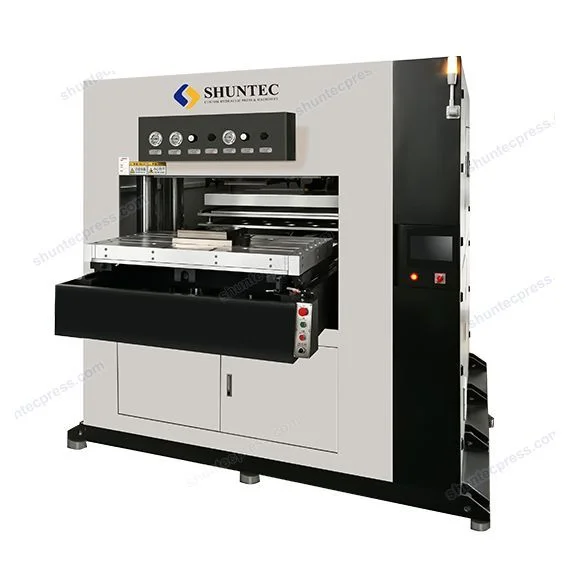
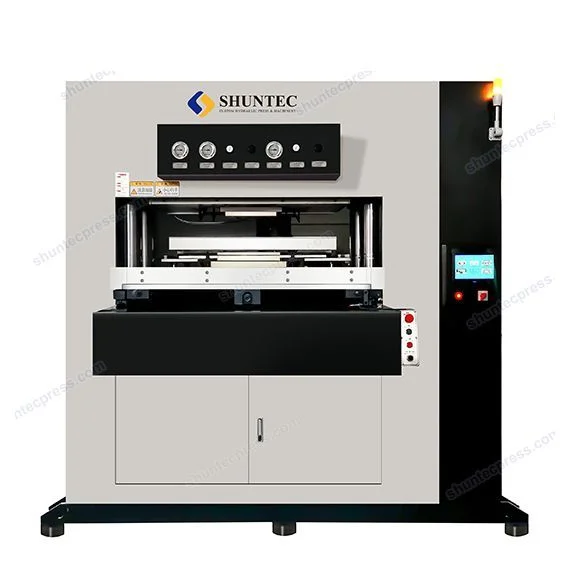
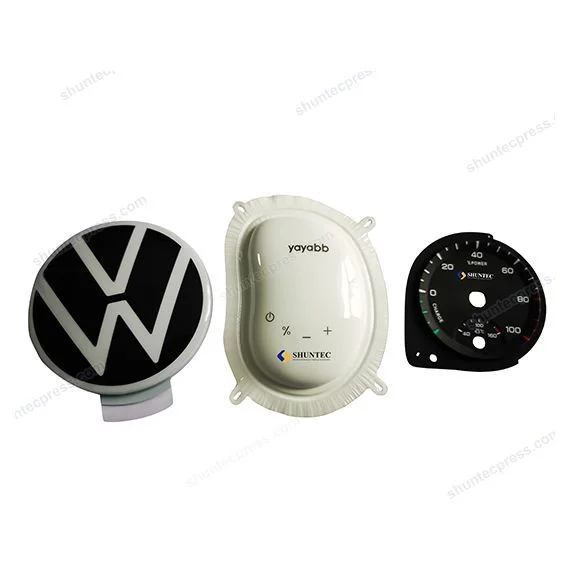
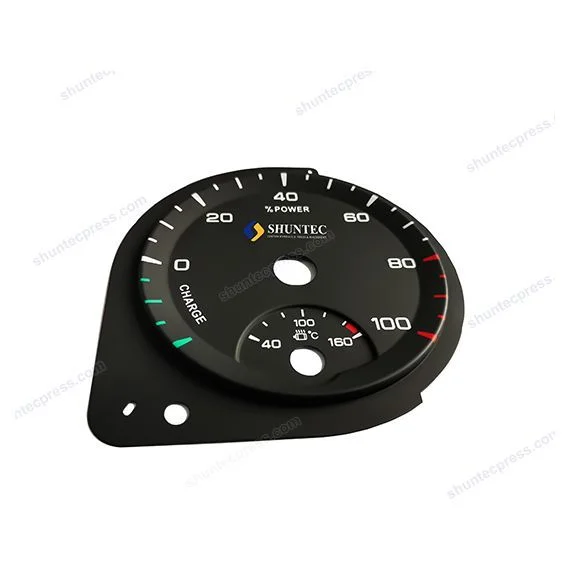
Pressurized Air Bulge Forming Press
Shuntec’s pressurized air bulge forming presses are ideal for manufacturing parts from a variety of sheet/film materials including composite sheet films such as PC/PMMA/ABS, glass fiber, carbon fiber, and many other sheets/films. Using a Shuntec pressurized air bulge forming press, you can produce sheets/films with complex and non-symmetrical features while maintaining uniform wall thicknesses.
Have custom requirements? We can customize an Pressurized Air Bulge Forming Press according to your needs. SHUNTEC’s Pressurized Air Bulge Forming Press are designed for high performance and reliability, offering comprehensive support from design to after-sales service.
We ensure the safe and efficient transportation of our custom hydraulic presses, taking into account their size, weight, and sensitivity.
Our team coordinates with trusted logistics partners to handle every detail, from packing and securing the equipment to international shipping and delivery.
Each press is carefully packaged to prevent damage during transit, and we offer tracking and support throughout the shipping process, ensuring timely and secure arrival at your designated location.
- Machine Video
- Machine Highlight
- Machine Specifications
- Machine Options
Nowadays, the product appearance of electronics and automobiles is getting more and more beautiful and complex. Take the mobile phone as an example, the back cover of the mobile phone is gorgeous with new multilayers printing processes. And the complex R angle is the popular and common design for the mobile phone back cover. So, it is important to quickly form the sheet/film with a complex shape before IMD forming process.
Shuntec’s pressurized air bulge forming press is newly designed and developed for composite sheet/film hot forming. And it is becoming increasingly popular among manufacturers because of its ability to produce seamless, lightweight, “near-net-shape” parts. During the pressurized air bulge forming process, operators insert a blank into a mold. The special heating device of the press quickly heats the blank to its softening temperature, with optional maximum heating temperature ranges from 600 ℃ to 1000 ℃. Then, the press introduces pressurized air into the chamber. The pressurized air presses from top to bottom with the segmented high pressure, while the lower mold cavity is evacuated. The pressurized air forms the material to the shape and contour of the tool so that the film material is perfectly and accurately formed and molded into a complex shape.
Throughout this process the press acts as a clamp, applying force to the tool in order to counter the pressure being injected into the chamber, ensuring the tool remains closed. The air pressure and holding time can be adjusted separately. There is no upper mold, only a lower mold. There will be no problem with film surface scratches caused by direct contact with the mold on the film surface. The residual stress of the formed film is at a very low level. The corners of the composite material do not turn white after forming, while the printed layers are continuously layered, and do not separate.
Product Datas
Applicable Industries | Sheet/film material hot forming with complex shape, widely used in 3C industry, home appliance industry, electronics industry, automobile industry. |
Production Lead-time | About 30~55 workdays |
Power Supply | Three-phase, 220V/380V/415V/480V/600V, 50/60 HZ optional; Custom made to your requirement |
Customizable | Highly customized to your requirements |
Packing | Wooden package suitable for sea transport |
Aftersales Service | Field installation/maintenance/repair, commissioning and training, free spare parts, video technical support |
Warranty | 18 months |
Payment Term | T/T |
Delivery Term | EXW, FOB,CFR,CIF,DDU |
Certification | CE/UL/ISO |
Technical Parameters
Items | For Mobile Phone Industry | For Automobile Industry | |
Model | Shuntec-AHGm-100T | Shuntec-AHGa-100T | |
Nominal Force | 100 Ton | 100 Ton | |
Hydraulic Pressure | 21 MPa | 21 MPa | |
Return Force | 5 Ton | 5 Ton | |
Height of the Bed Table Above Floor | 1150 mm | 1150 mm | |
Daylight | 500 mm | 600 mm | |
Stroke | 300 mm | 400 mm | |
Bed Table Size | 600 (between columns) * 550 mm | 800 (between columns) * 500 mm | |
Slider Speed | Up-acting | 100~130 mm/s | 100~130 mm/s |
Pressing | 10~14 mm/s | 10~14 mm/s | |
Return | 150~180 mm/s | 150~180 mm/s | |
Overall Dimensions | 1280*1430*2300 mm | 1530*1600*2400 mm | |
Servo Motor Power | 16 KW | 16 KW |
• Servo-hydraulic control system
• Automated loading and unloading system
• Interlocked, hinged guards on 3 sides
• Portable operator console
• Color HMI
• Linear position sensor
• Load cell
• Automatic tie bar lubrication
• IR (infrared) non-contact heating device
• Preheating chamber
• Multi-point PID temperature accurate control
• Preheating chamber with ceramic heating bricks, which can heat the special material up to 600°-1000° in a few seconds
• 20 sets of technical formula storage capacity
Shuntec's most popular custom hydraulic press machines