Manufacturing has always been a bedrock of civilization, an essential part of human progress, and a vital component of our everyday lives. From the car parts we use to the ceramic tiles that adorn our homes, the influence of manufacturing is undeniable. One tool that plays a significant role in the manufacturing industry is the hydraulic press. The hydraulic press has proven indispensable, especially in the production of ceramics. This article aims to provide an in-depth look at how hydraulic presses are used to make ceramics, the advantages they bring, and the principle upon which they operate.


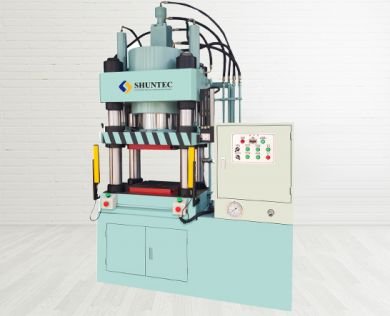
Understanding the Hydraulic Press and How It Works
A hydraulic press is a machine that uses hydraulic cylinders driven by the pressure of a fluid—typically oil—to generate a compressive force. This machine operates based on Pascal's principle, which states that pressure exerted anywhere in a confined fluid is transmitted equally in all directions, with no loss and acting with equal force on equal areas.
The primary components of a hydraulic press include the hydraulic cylinders, hydraulic fluid, power supply, and pressing plates or dies. The hydraulic cylinders, often two in number, are essential parts of the hydraulic system, providing the pressing force necessary for the operation of the press. The hydraulic fluid, typically an oil, is the medium through which pressure is transmitted within the system. The power supply is the engine that drives the entire process, often an electric motor or an engine that powers a pump, which then pressurizes the hydraulic fluid.
When the hydraulic press is in operation, the hydraulic fluid is forced into the cylinder by the pump, causing the piston inside the cylinder to move. This movement is then transferred to the pressing plates or dies, which exert a compressive force onto the material placed between them. The force exerted is directly proportional to the pressure applied to the fluid.
In a typical hydraulic press setup, there are two cylinders: a smaller one where the hydraulic fluid is initially pressurized, and a larger one where the fluid's pressure is used to move the piston. The disparity in their sizes allows the press to amplify force, enabling it to generate a high level of pressure with relatively little input force.
Why Hydraulic Presses are Preferred over Mechanical Presses
Hydraulic presses have several advantages over their mechanical counterparts, making them a preferred choice in many industries.
Firstly, hydraulic presses are capable of delivering the same power throughout the entire stroke length. This contrasts with mechanical presses, where the force varies depending on the position of the ram in the stroke cycle. This consistent pressing force ensures better quality control and uniform products.
Secondly, hydraulic presses require less manual effort compared to traditional methods such as manual hammering. The hydraulic system does the heavy lifting, allowing the operator to focus on controlling the process. This not only increases efficiency but also reduces worker fatigue and the potential for injury.
Thirdly, hydraulic presses offer precision that is unmatched by mechanical presses. Precise control over the pressing force and stroke length allows for accurate shaping and forming of materials—a critical requirement in industries such as the medical industry, food industry, and high-precision manufacturing.

Hydraulic Presses and Their Uses
Hydraulic presses have found uses in a variety of industries, owing to their versatility, precision, and power. They play a key role in shaping panels for airplane body panels, pressing vehicle parts in repair shops, and manufacturing essential components like oil filters and windshield wiper blades in the automobile industry.
In the food industry, hydraulic presses are used to extract juices from fruits and vegetables, making food easier to digest. They also find use in shaping and packaging food products, ensuring a longer shelf life.
In the medical industry, hydraulic presses are used for compressing pills and tablets from powdered compounds, ensuring the proper dosage of medication is delivered in each unit. Their precision and consistency are crucial in this field where a slight variation can have significant health implications.
Hydraulic presses also have military applications. They are employed in the production of armor plates, ammunition, and various components of military-grade vehicles and weapons systems. The durability and high pressure provided by hydraulic presses are vital in creating robust and reliable military equipment.
In the manufacturing industry, hydraulic presses are instrumental in the production of gear assemblies and gear housings. They are also used in the production of electrical parts, shaping metal plates into various forms with high precision and consistency. The ability of hydraulic presses to work with various materials, from metals to plastics, makes them indispensable in the manufacturing sector.
The Role of Hydraulic Presses in the Ceramics Industry
Hydraulic presses have had a profound impact on the ceramics industry. The hydraulic press replaced the old, labor-intensive methods of shaping ceramics, providing a more efficient and controlled process. The precision, power, and adaptability of hydraulic presses make them ideal for shaping a variety of ceramic products.
The ceramic production process starts with raw materials, usually a mixture of clay, kaolinite, feldspar, and silica. These raw materials are ground into a fine powder and mixed with water to form a ceramic paste. The ceramic paste is then placed in a die or mold, and the hydraulic press is used to exert a high-pressure force onto the paste, causing it to take the shape of the mold.
This pressing process allows for the production of various ceramic products, from ceramic tiles to bathroom tiles, with great precision and consistency. Hydraulic presses are also used to create intricate artistic ceramics, offering an artistic control that was previously difficult to achieve with manual methods.
Moreover, hydraulic presses are used to make advanced ceramics for industrial applications. Advanced ceramics have properties that make them suitable for use in extreme conditions, such as high temperatures, corrosive environments, or high wear situations. These include ceramics used in the production of engine components, armor platings, and fuel cell compression.
One of the main advantages of using a hydraulic press in ceramic production is its ability to apply uniform pressure. This even pressure distribution helps to minimize defects in the ceramic material, improving the quality and strength of the final product.

Hydraulic Presses and the Environment
Environmental considerations are an essential part of any manufacturing process, and hydraulic presses are no exception. These machines use hydraulic fluid, typically oil, to transmit pressure. The management of this oil, particularly its disposal, is a critical aspect of operating a hydraulic press.
Used hydraulic fluid can be contaminated with metal shavings, dirt, and other impurities. It can't be simply dumped into the environment due to its potential to harm both terrestrial and aquatic life. Therefore, waste oil from hydraulic presses must be collected and properly disposed of according to local environmental regulations. Some hydraulic press operators opt to recycle their used oil, filtering it to remove impurities so it can be reused.
Hydraulic presses also contribute positively to environmental preservation by enhancing resource efficiency. By delivering consistent, high-pressure force, they ensure that raw materials are used optimally, reducing waste.
Moreover, by replacing manual labor, hydraulic presses minimize the human error that can result in defective products, thus reducing wastage. Their high precision and consistency ensure that every bit of raw material translates to a quality product, thereby contributing to sustainable manufacturing practices.
Conclusion
Hydraulic presses have revolutionized the manufacturing industry, providing an efficient, precise, and powerful tool for shaping and forming various materials. Their impact on the ceramics industry has been particularly profound, replacing labor-intensive manual methods with a more efficient and controlled process.
With their ability to deliver uniform pressure and high force, hydraulic presses have improved the quality and consistency of ceramic products, from everyday items like ceramic tiles and bathroom fixtures to specialized applications in the automotive and aerospace industries. They have also enabled the creation of intricate artistic ceramics, providing a level of control and precision previously difficult to achieve with manual methods.
Moreover, hydraulic presses have demonstrated their versatility, finding uses in diverse industries. From shaping panels for airplane body panels in the aerospace industry to manufacturing oil filters and windshield wiper blades in the automotive sector, hydraulic presses have proven indispensable. Their role in the food industry, in making food easier to digest and extending its shelf life, and their utility in the medical industry, where they are used to compress pills and tablets, further underline their importance.
Environmental considerations have been an important aspect of operating hydraulic presses. The disposal of used hydraulic fluid, typically oil, must be carefully managed to prevent environmental harm. Fortunately, many operators opt for recycling, ensuring that the oil is filtered and reused, thus promoting sustainability.
In conclusion, hydraulic presses have had a great success in the manufacturing industry, significantly transforming the production process. Their power, precision, and versatility have made them an invaluable tool, not just in the ceramics industry, but in a wide array of sectors. Their continued use promises further advancements and efficiencies in manufacturing, underscoring the irreplaceable role they play in shaping the world around us.